Comprehending What is Porosity in Welding: Reasons and Solutions
Wiki Article
Recognizing Porosity in Welding: Discovering Reasons, Impacts, and Avoidance Techniques
As experts in the welding market are well conscious, recognizing the causes, results, and prevention techniques associated to porosity is critical for achieving robust and trusted welds. By delving right into the origin creates of porosity, analyzing its detrimental results on weld high quality, and checking out efficient avoidance approaches, welders can boost their knowledge and abilities to generate top quality welds constantly.Common Reasons For Porosity
Contamination, in the kind of dirt, oil, or corrosion on the welding surface, produces gas pockets when warmed, leading to porosity in the weld. Incorrect shielding occurs when the securing gas, typically made use of in processes like MIG and TIG welding, is not able to totally protect the molten weld pool from responding with the bordering air, resulting in gas entrapment and subsequent porosity. Furthermore, inadequate gas insurance coverage, frequently due to inaccurate circulation prices or nozzle positioning, can leave parts of the weld unguarded, allowing porosity to form.Impacts on Weld Top Quality
The visibility of porosity in a weld can substantially compromise the general top quality and honesty of the welded joint. Porosity within a weld creates spaces or tooth cavities that deteriorate the framework, making it much more prone to breaking, corrosion, and mechanical failure.Furthermore, porosity can prevent the efficiency of non-destructive testing (NDT) methods, making it challenging to spot other problems or interruptions within the weld. This can cause substantial security issues, especially in essential applications where the architectural stability of the bonded elements is paramount.

Avoidance Techniques Overview
Given the harmful effect of porosity on weld high quality, efficient avoidance strategies are crucial to maintaining the structural integrity of bonded joints. Additionally, selecting the suitable welding parameters, such as voltage, current, and travel rate, can aid minimize the risk of porosity development. By including these avoidance strategies right into welding techniques, the event of porosity can be substantially minimized, leading to more powerful and much more trusted welded joints.Value of Appropriate Shielding
Correct securing in welding plays a critical role in stopping atmospheric contamination and making sure the stability of welded joints. Securing gases, such as argon, helium, or a mix of both, are typically used to shield look what i found the weld swimming pool from reacting with components in the air like oxygen and nitrogen. When these reactive elements come right into contact with the hot weld swimming pool, they can create porosity, leading to weak welds with lowered mechanical properties.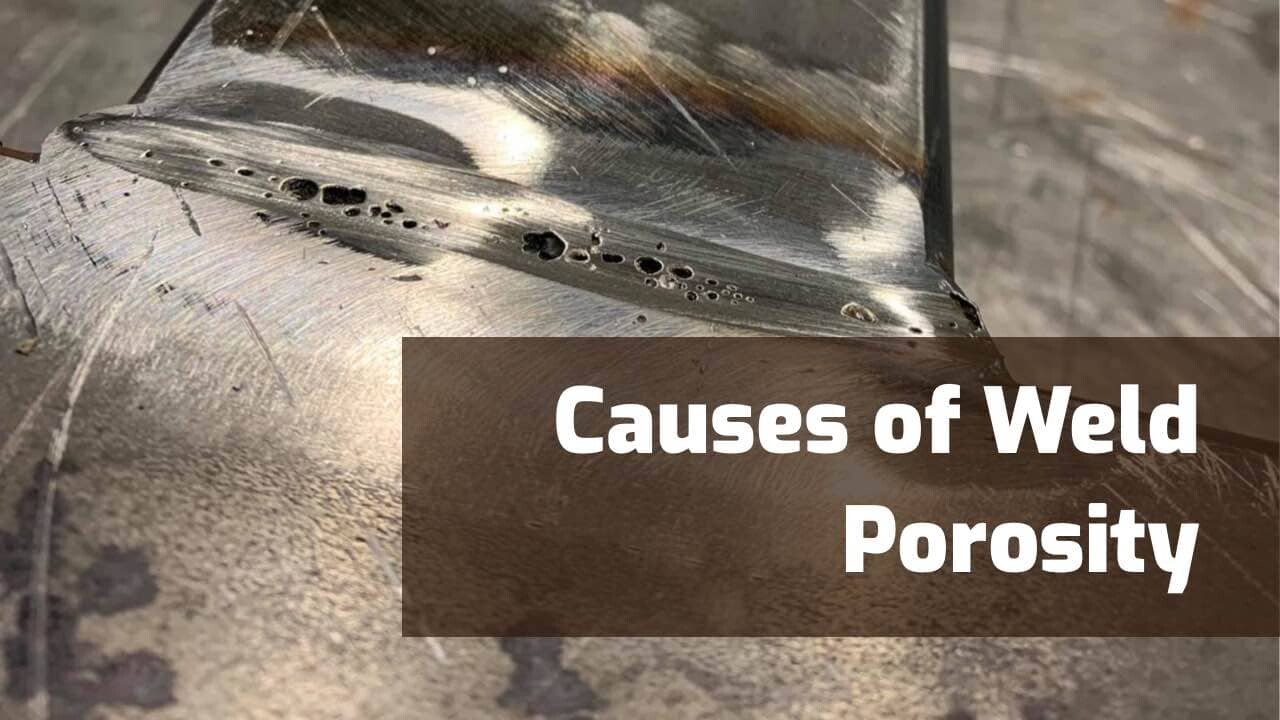
Insufficient securing can lead to various flaws like porosity, spatter, and oxidation, jeopardizing the architectural integrity of the bonded joint. Therefore, adhering to appropriate shielding methods is essential to create top quality welds with marginal problems and make certain the longevity and dependability of the bonded components (What is Porosity).
Surveillance and Control Methods
How can welders effectively check and control the welding process to make sure optimum outcomes and prevent problems like porosity? One trick method is via the use of advanced tracking innovations. These can include real-time surveillance systems that offer responses on specifications such as voltage, existing, take a trip rate, and gas circulation prices. By continually keeping track of these variables, welders can determine variances from the optimal problems and make instant modifications to avoid porosity formation.
Furthermore, carrying out appropriate training programs for welders is necessary for keeping an eye on and managing the welding process effectively. What is Porosity. Enlightening welders on the value of keeping regular specifications, such as proper gas shielding and take a trip speed, can aid prevent porosity concerns. Normal analyses and qualifications can also make certain that welders excel in surveillance and managing welding processes
Moreover, making use of automated welding systems can boost tracking and control abilities. These systems can exactly manage welding specifications, reducing the probability of human error and making sure regular weld top quality. By combining innovative monitoring innovations, training programs, and automated systems, welders can effectively keep an eye on and manage the welding procedure to reduce porosity issues and achieve high-grade welds.
Conclusion

Report this wiki page